π 3D Additive Manufacturing Conference – 1st Edition
π October 06-10, 2025
πΒ Palacio Miramar, San Sebastian (Spain)
π Centro Carlos SantamarΓa, San Sebastian (Spain)
π Website 3dam-conference.com
π Linkedin @3dam2025-conference
π Instagram @3dam2025_sansebastian
From new printing technologies to the integration of digital design, to multiscale simulations, artificial intelligence and machine learning, multimodality manufacturing methods, material synthesis, multi-material printing, composite manufacturing, and performance engineering materials, all researchers are invited to join us in the beautiful Donostia / San SebastiΓ‘n, Spain, from the 6th to the 10th of October 2025.
In addition to plenary, keynote and invited talks, the conference has designated time for oral presentations and poster sessions from individuals of all career stages, and a one day Symposium for Young Scientists on the 6th to facilitate the collaboration between a new generation of scientists working in AM technologies.
Concept and Organization
This conference focusing on AM of soft materials assembles diverse communities of researchers from both academia and industry, with the aim of covering a broad scope of angles from new printing technologies and the integration of digital design, to multiscale simulations, artificial intelligence and machine learning, multimodality manufacturing methods, material synthesis, multi-material printing, composite manufacturing, and performance engineering materials.
AM invites a diverse cadre of researchers, from sustainability scientists and manufacturing engineers to entrepreneurs, as well as drawing on a wide range of materials expertise β from thermosets, vitrimers, and thermoplastics to hydrogels, organogels, and composites β for various AM technologies.
ORGANIZING
Haritz Sardon / POLYMAT, University of the Basque Country, Spain
Eva Blasco / Heidelberg University, Germany
Timothy Long / Arizona University, USA
SCIENTIFIC COMMITTEE
Haritz Sardon / POLYMAT, University of the Basque Country, Spain
Eva Blasco / Heidelberg University, Germany
Tim Long / Arizona University, USA
David Mecerreyes / POLYMAT, University of the Basque Country, Spain
Tao Xie / Zhejiang University, China
Lorenzo Moroni / Maastricht University, Netherlands
Callie Higgins / National Institute of Standards and Technology (NIST), Colorado, USA
Qin Xiao-Hua / ETH Zurich Switzerland
Katharina Ehrmann / Institute of Applied Synthetic Chemistry, TU Wien, Austria
Emily Pentzer / Texas A&M University, USA
Katrien Bernaerts / Maastricht University, Netherlands
Riccardo Levato / Utrecht University, Netherlands
Daryl Yee / EPFL Losanne, Switzerland
Zachariah Page / University of Texas at Austin USA
Program and speakers
PLENARY SPEAKERS
Tim Long / Arizona University, USA
David Mecerreyes / POLYMAT, University of the Basque Country, Spain
Tao Xie / Zhejiang University, China
Emily Davidson / Princeton University, New Jersey, USA
Sandra Van Vlierberge / Ghent University, Belgium
Martin Wegener / KIT, Germany
KEYNOTE AND INVITED SPEAKERS
Keynote and invited speakers include reaserchers with both academic and industrial backgrounds.
Please find the full list of speakers and their updated biographies on our website: https://3dam-conference.com/speakers/
PROGRAM
π£ One day Young Researchers Symposium
π€Plenary lectures by David Mecerreyes, Sandra Van Vlierberghe, Martin Wegener, Tao Xie, Emily Davidson, Tim Long
π 2 poster sessions
πCall for abstract with 50 oral presentation from all careers researchers in AM
π€ Keynote and invited lectures from both industrial and academic researchers
π Awards for the best posters ans speeches
π High scientific quality contributions
π΄ Free lunch and two coffee breaks everyday
π Free social activities
π₯ Gala dinner
π Great location!
Check our website for the full program!
Collabs and partners
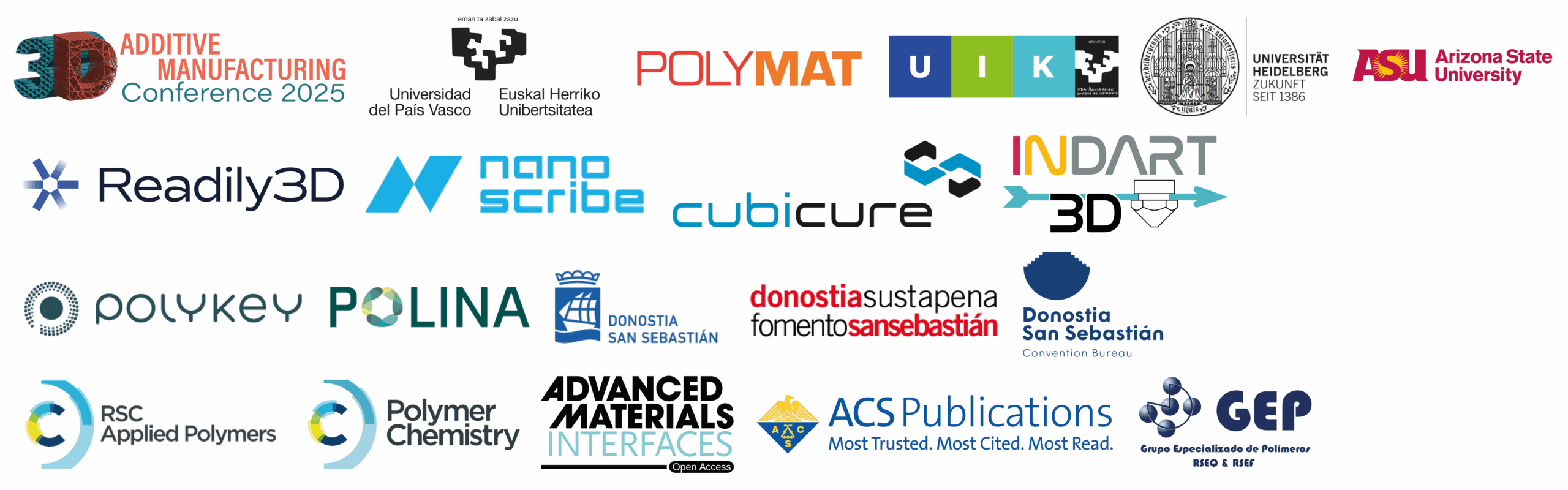
Check all our partners on our website: 3dam-conference.com/collabs